Veneer logs are available from over 80 countries worldwide in both hardwood and softwood. They are sliced in the United States, North America, South America, Europe, Asia and Africa. The majority of veneer in America is sliced domestically or in Europe. In dealing with projects both large and small, it is advisable to develop a relationship with an AWI member woodworker or a veneer supplier. You can rely on them for expertise in availability, durability and pricing.
Sampling
This is a very important part of the process of the selection and specification process. The samples have to be pulled in such a way that when reviewed by a designer and/or mill worker they represent the overall appearance of the veneer. It is encouraged that no project be specified from a 12" x 12" panel. The purpose of the panel is to show a particular veneer with a finish. Once that has been established, then the full sample set should be seen to show the veneer in full length.
The standard in the industry is to pull a sample about every 1,000 sq. ft. This applies more for domestic species. The larger exotic species, such as bubinga and sapele, are sampled according to any changes that occur from the beginning to the end.
Often three samples will be pulled from a given stack such as the full tree restacked (a figured cherry) shown below. 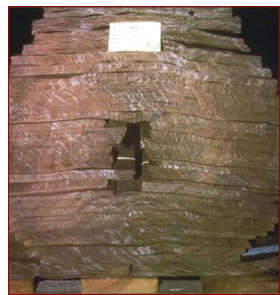 In this case a sample was pulled from the front section, another from the middle, and a third from the back section. Additional samples could be pulled by the veneer vendor if it was felt to be necessary.
Proper sampling ensures that what you see is what you get! Of course in any project if it is possible to inspect the veneer bundle by bundle, and that is the ultimate. Since this is the exception rather than the rule, sampling correctly is very important.
The first issue in the selection process is to define the scale of the project accurately. If it is of relatively small scale, the veneer will probably be available in a large number of species from a large number of suppliers. As the scale increases, the availability of veneer species may decrease, and the necessity for multiple flitches will increase. For instance, manufacturing elevator lobbies for a 40-story office building does not require that flitches for each floor match the adjacent floors, and smaller flitches can be used, whereas a symphony hall may require multiple flitches, all matching each other since it is viewed as a whole.
The width of the leaves in a flitch can vary from wide to narrow, and the leaves may need to be selected or assigned to specific areas of a project. When selecting multiple flitches it is important to note the grain, color and characteristics of each flitch and compare them to adjacent flitches which may be seen together. The design professional should work closely with the woodworker and veneer supplier to communicate the intent of the design. The woodworker can provide an understanding and awareness for the design professional of the constraints of the natural material along with diligence in the selection process that can produce monumentally beautiful woodwork. Wood's character, color, grain, texture and matching are tools in the designer's pallet that provide the desired appearance.
It is tremendously beneficial, especially when schedule is important, for the design professional to pre-select the veneer prior to the bidding process. Failing that, as soon as a woodworker is selected, veneer samples should be reviewed and selected. It is the relationship between the design professional and the woodworker and veneer supplier where trust and understanding lead to an exemplary project.
In many cases, even after veneer is selected the interior of the bundles in a flitch may have gaps, splits, or other defects which require removal of many leaves from the center of the flitch, thus ruining a discrete match between leaves. In cases such as this it should be understood that waste factors increase and cost will increase as well.
Thus it is the responsibility of the professional who selects the flitches to "turn" the flitch or go through each bundle so that these defects are known prior to selection. |